Product Introduction
spade drill inserts
When processing workpieces of different materials, choose spade drill bits of different materials for processing.
The spade drill insert material is divided into
1. Carbide (Φ9.5mm~Φ47.5mm) adopts Balzers coating
2. Powder high-speed steel (Φ9.5mm~Φ114.0mm)
3. Cobalt-containing high-speed steel (Φ9.5mm~Φ114.0mm)
When processing workpieces of different materials, choose spade drill bits of different materials for processing.
The spade drill insert material is divided into
1. Carbide (Φ9.5mm~Φ47.5mm) adopts Balzers coating
2. Powder high-speed steel (Φ9.5mm~Φ114.0mm)
3. Cobalt-containing high-speed steel (Φ9.5mm~Φ114.0mm)
Inserts of three materials with the same diameter can be installed on the same spade drill arbor.
It can greatly reduce the customer's purchase cost on the tool holder.
It can greatly reduce the customer's purchase cost on the tool holder.
1. It is recommended to use high-speed steel and powdered high-speed steel inserts for vertical drills and radial drills.
It is not recommended to use carbide inserts. The machine tool speed is low, the rigidity is poor, and the gap is large, which can easily cause the carbide insert to jump.
2. All spade drill tool holders have a central water outlet. It is recommended to use high-pressure internal coolant as much as possible. This will greatly extend the service life of the insert and is more conducive to chip removal.
3. All spade drill inserts are designed with chip breakers, and the processed iron chips are all small chips. Compared with the long chips processed by traditional twist drills, small chips are easier to remove without the need to retreat to break chips. , can be hit to the bottom to shorten the processing time and improve processing efficiency.
4. The spade drill insert has a self-centering function, and the double-edged inserts bear symmetrical and even force, making it suitable for processing deep holes.
Calculation of spade drilling processing parameters
The linear speed of the drilled high-speed steel and powdered high-speed steel inserts is 20-40 meters.
The linear speed of the carbide insert is 50-60 meters, and the feed per revolution of the spade drill insert can reach 0.1-0.6mm per revolution.
The linear speed of the drilled high-speed steel and powdered high-speed steel inserts is 20-40 meters.
The linear speed of the carbide insert is 50-60 meters, and the feed per revolution of the spade drill insert can reach 0.1-0.6mm per revolution.
A. The formula for calculating drilling rate is: S=VC*1000/3.14/Dc
(S is the rotation speed, Vc is the linear speed, and Dc is the insert diameter)
B. The feed calculation formula is: Vf=Fr*S
(Vf is feed, Fr is feed per drill, S is rotation speed)
The C processing time formula is: Tc=H/Vf*60
(Tc is processing time, H is hole depth, Vf is feed)
(S is the rotation speed, Vc is the linear speed, and Dc is the insert diameter)
B. The feed calculation formula is: Vf=Fr*S
(Vf is feed, Fr is feed per drill, S is rotation speed)
The C processing time formula is: Tc=H/Vf*60
(Tc is processing time, H is hole depth, Vf is feed)
Speed and feed calculation examples
Processing diameter 20mm, depth 100mm,
Choose powdered high-speed steel inserts, and the linear speed is calculated as 40 meters.
S=40*1000/3.14/20=636 (recommended drilling speed per minute is
F600-650 or so)
Vf=0.2*636=127 (recommended feed per minute is S110-130
about)
Tc=100/127*60=47 (processing time is about 50 seconds)
Processing diameter 20mm, depth 100mm,
Choose powdered high-speed steel inserts, and the linear speed is calculated as 40 meters.
S=40*1000/3.14/20=636 (recommended drilling speed per minute is
F600-650 or so)
Vf=0.2*636=127 (recommended feed per minute is S110-130
about)
Tc=100/127*60=47 (processing time is about 50 seconds)
Precautions for use
1. When using a spade drill, there must be a central water outlet, which is beneficial to extending the tool life and providing better chip removal effect;
2. When using the tool for the first time, it is recommended to lower the parameters by 10-15% when just entering the tool and preparing to drill through.
3. If the length exceeds 8D, a pilot hole of the same diameter must be pre-drilled before use. The depth of the pilot hole is 1-2 times the hole diameter, which can greatly reduce the problem of drill bit deviation.
4. The drilled iron slag is generally in the shape of fragments. Pay attention to the sound and the shape of the iron slag during processing. If strips of iron slag appear, the usage parameters must be adjusted in time;
5. When processing a through hole, retract the tool when the hole is drilled. Be careful not to completely extend the insert out of the hole to avoid damage caused by the insert hitting the workpiece when retracting;
1. When using a spade drill, there must be a central water outlet, which is beneficial to extending the tool life and providing better chip removal effect;
2. When using the tool for the first time, it is recommended to lower the parameters by 10-15% when just entering the tool and preparing to drill through.
3. If the length exceeds 8D, a pilot hole of the same diameter must be pre-drilled before use. The depth of the pilot hole is 1-2 times the hole diameter, which can greatly reduce the problem of drill bit deviation.
4. The drilled iron slag is generally in the shape of fragments. Pay attention to the sound and the shape of the iron slag during processing. If strips of iron slag appear, the usage parameters must be adjusted in time;
5. When processing a through hole, retract the tool when the hole is drilled. Be careful not to completely extend the insert out of the hole to avoid damage caused by the insert hitting the workpiece when retracting;
Product details
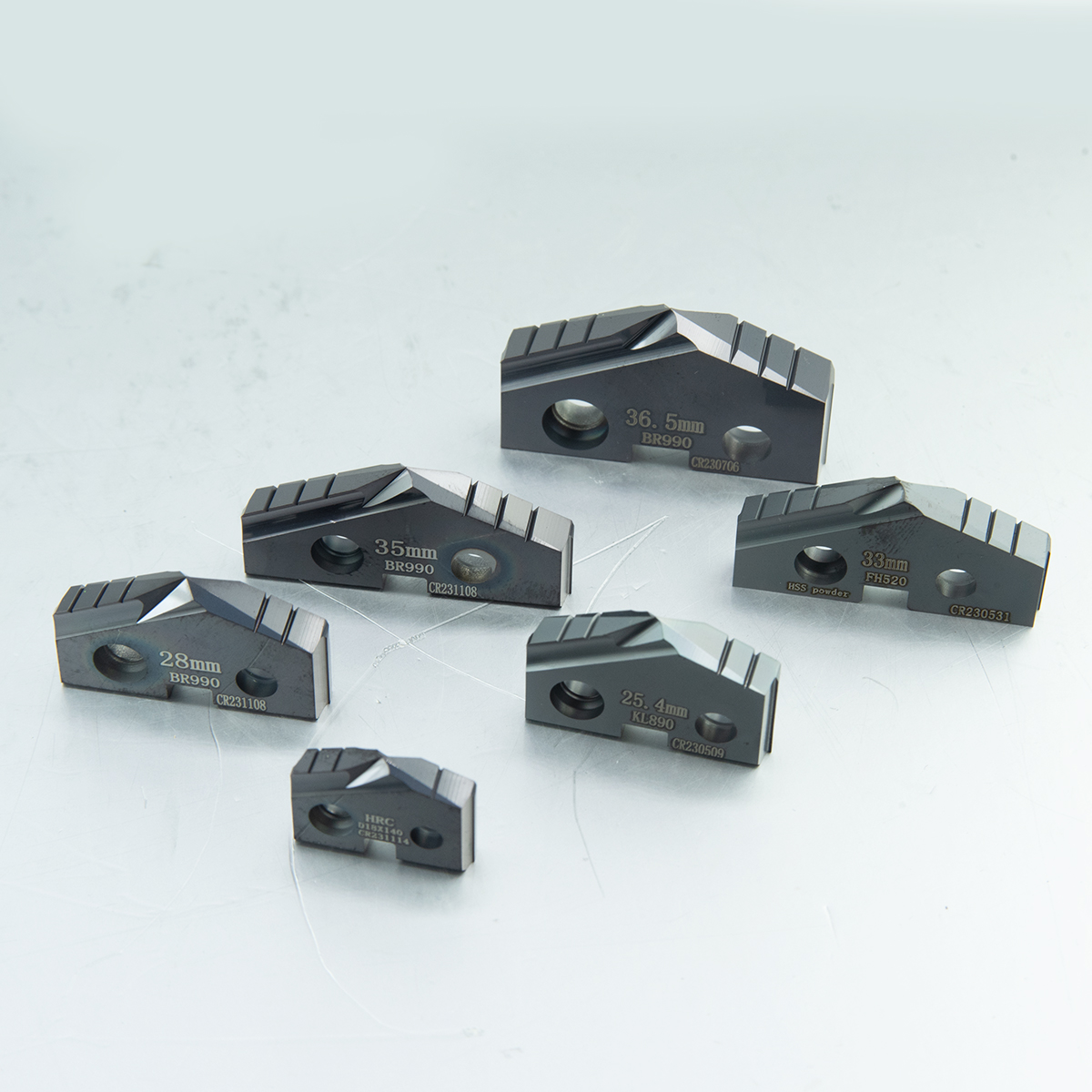
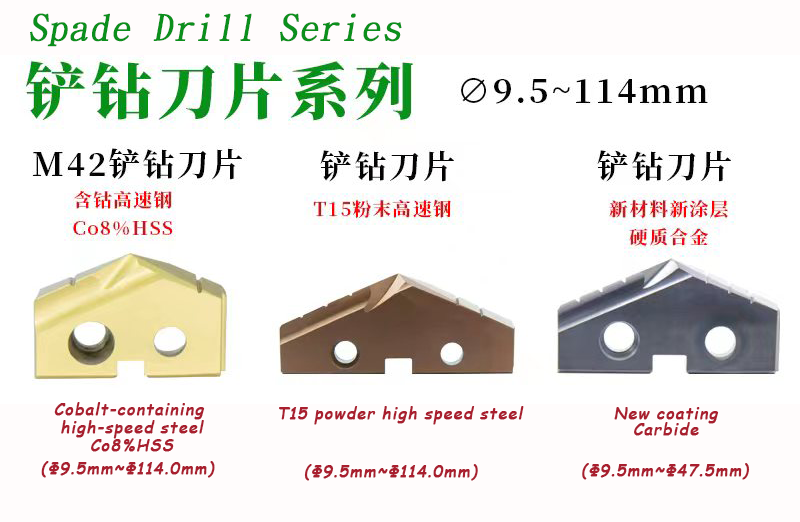
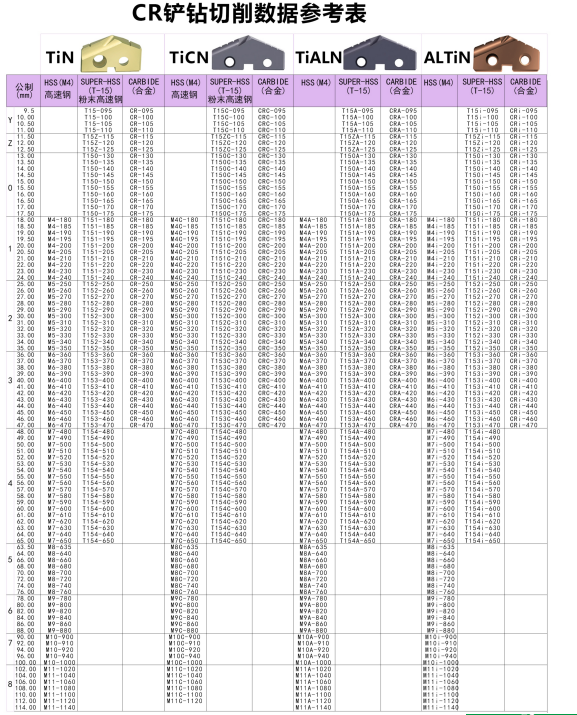
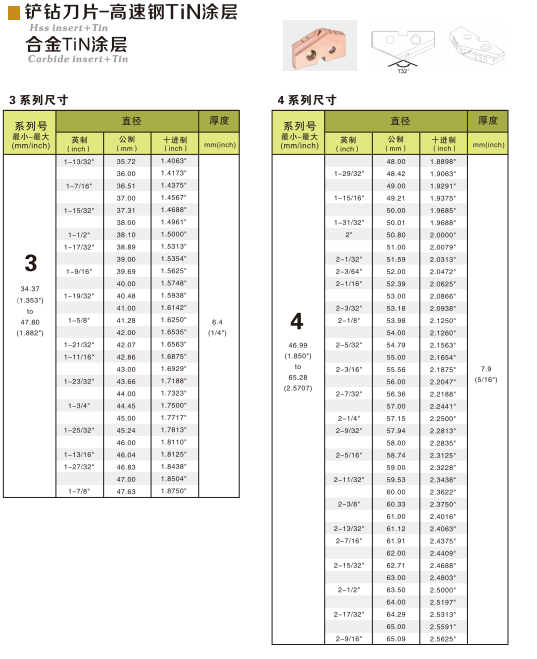
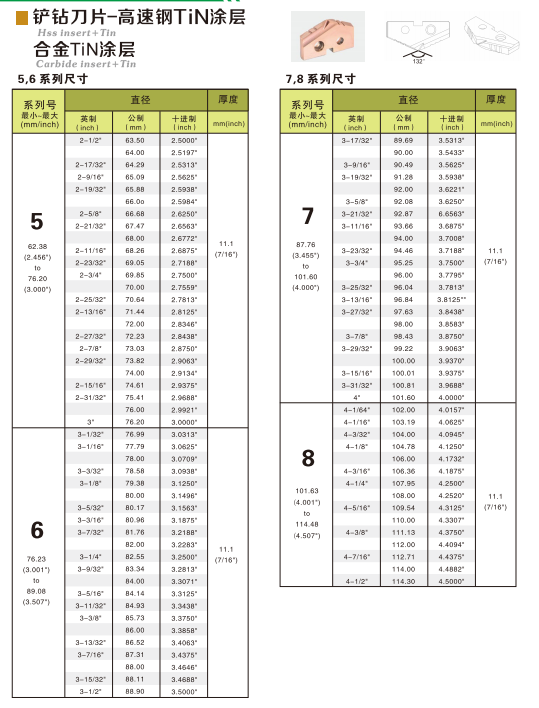
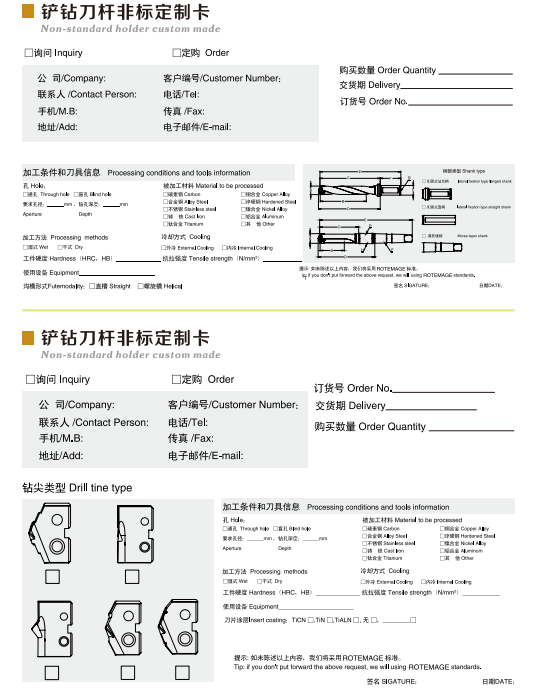