Essential details
Shipping:Express Delivery, Air freight, Land freight, Ocean freight
Specification Number:CR00~00-00-C00
Product Introduction
Spade drill holders
Diameter Range: ø9.5mm~~ø114mm
Effective length:
50/70/100/150/200/250/300/
350/400/450/500mm
The insert design is suitable for deep hole machining.
The spiral insert design and central water outlet (internal cooling) optimize the chip removal function.
A single tool holder can be used with multiple specifications of inserts, which is economical.
*The length of the tool bar can be customized according to processing needs.
Spade drill insert mold blank spot
Conventional production below 48MM
(including 48MM)
Conventional inserts produce
integers and 0.5
decimals can also be produced
according to customerneeds.
Delivery time is generally 2-3 days
Diameter Range: ø9.5mm~~ø114mm
Effective length:
50/70/100/150/200/250/300/
350/400/450/500mm
The insert design is suitable for deep hole machining.
The spiral insert design and central water outlet (internal cooling) optimize the chip removal function.
A single tool holder can be used with multiple specifications of inserts, which is economical.
*The length of the tool bar can be customized according to processing needs.
Spade drill insert mold blank spot
Conventional production below 48MM
(including 48MM)
Conventional inserts produce
integers and 0.5
decimals can also be produced
according to customerneeds.
Delivery time is generally 2-3 days
Instructions for use
Shovel drilling processing parameters
How to use tool holders with diameters of 8 times and above (same for vertical and horizontal types)
1. Guide hole processing
Use a short tool shank with the same diameter as the deep hole to create a pilot hole at least 2 times as deep as the diameter.
Use a blade with a tip angle that is the same as that of a deep-hole drill, or a blade with a larger angle than a deep-hole drill.
2. Insertion of deep hole drill bit
Set the rotation speed to 50RPM at most, fix the feed to F=300mm/min, turn off the coolant, and insert the deep hole drill bit 1~3mm from the end of the pilot hole under the above conditions.
3. When processing blind holes
The speed and feed are set to 100% of the recommended values. Please confirm the chip discharge status and the load rate of the machine tool while performing deep hole machining. Please do not use segmented feeding method for processing.
*If it is impossible to break the chips during actual processing, please use segmented processing. When feeding in sections, start with 4mm and gradually increase the length of the section processing.
*If the machine tool load rate changes drastically, it may be due to chip blockage. To prevent drill bit damage, please interrupt processing and review the cutting conditions and blade shape.
4. During through-hole processing (immediately before opening)
Before the drill tip is exposed, set the speed S to 50% of the recommended value and the feed F to 75% of the recommended value.
If the opening is an oblique hole, please make the same settings as above before any part of the drill bit is exposed.
The cutting edge of the drill bit must be exposed at least 3mm before the drill bit can be pulled out.
5. How to pull out the drill bit
When the drill bit is pulled out, the rotation speed is set to 50rpm at most
Precautions for deep hole processing process
*Be sure to drill 1D-2D pilot holes when using a shovel drill tool bar with a diameter of 8 times or above.
*Please use as much coolant as possible.
When there is vibration during cutting, it may cause the bolts to loosen.
At the beginning, please check the tightening of the bolts.
Mohs spade drill (requires cooling ring)
Precautions for using spade drill
1. Please tighten the blade tightening bolts evenly on the left and right
2. Do not touch the tip of the knife when preparing work
3. Please refer to the processing parameter table of the spade drill to confirm that the cutting speed, cutting feed vertical and horizontal types are the same.
Use a short tool shank to machine the pilot hole, and use the same insert as the 8x diameter and above tool shank to confirm chip disposal
Insert the pilot hole into the pilot hole with a tool bar that is 8 times or more in diameter and the same diameter as the pilot hole drill bit, rotate at low speed and feed quickly to start cooling
Carry out cutting rotation 1~2mm in advance and start cutting.
When cutting and discharging, confirm the load table of the mechanical equipment and perform cutting at the same time.
Low-speed rotation and speed feed return to the original position (refer to the photo below)
Precautions for deep hole processing process
*Be sure to drill 1D-2D pilot holes when using a shovel drill tool bar with a diameter of 8 times or above.
*Please use as much coolant as possible.
When there is vibration during cutting, it may cause the bolts to loosen.
At the beginning, please check the tightening of the bolts.
Product details
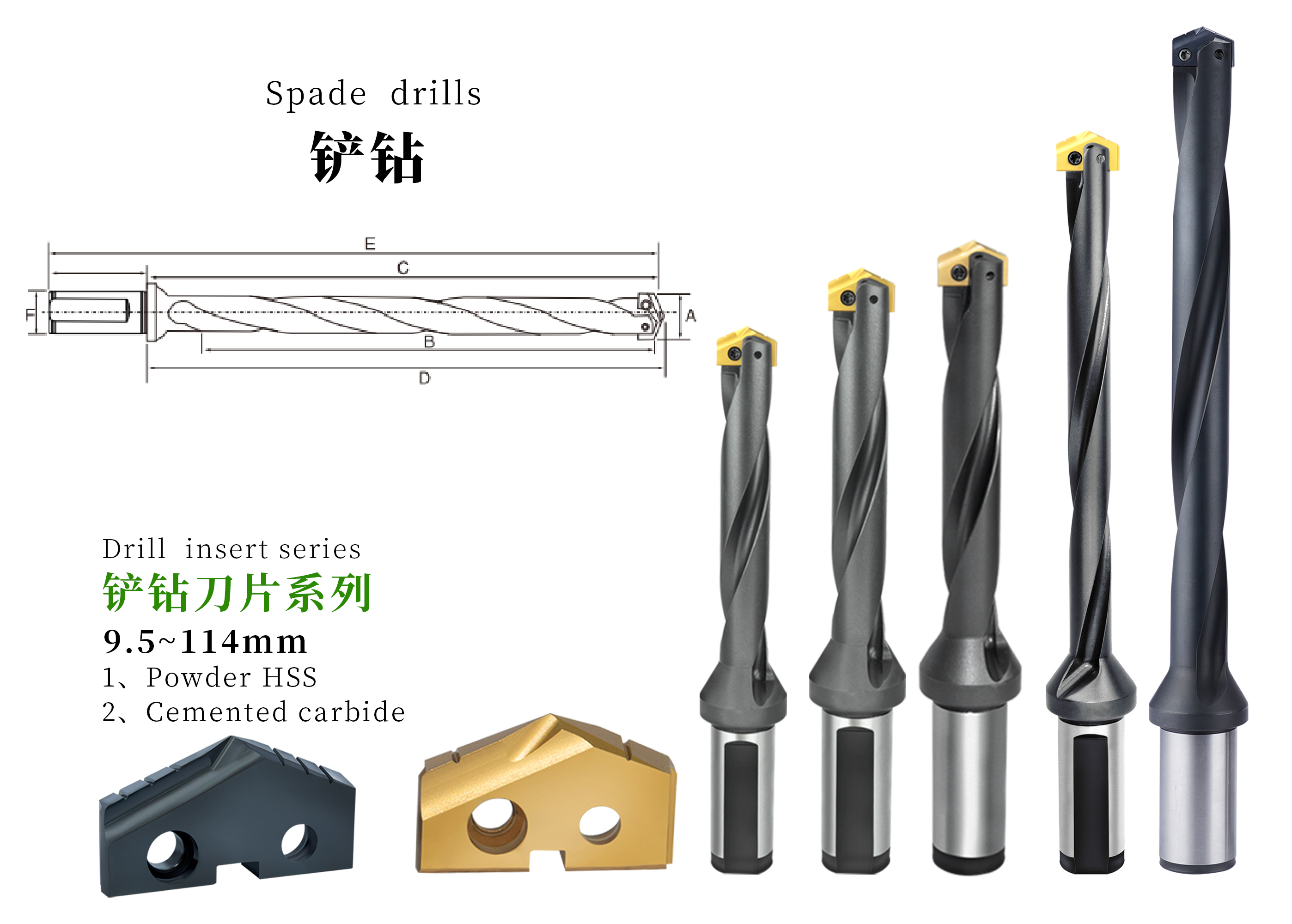
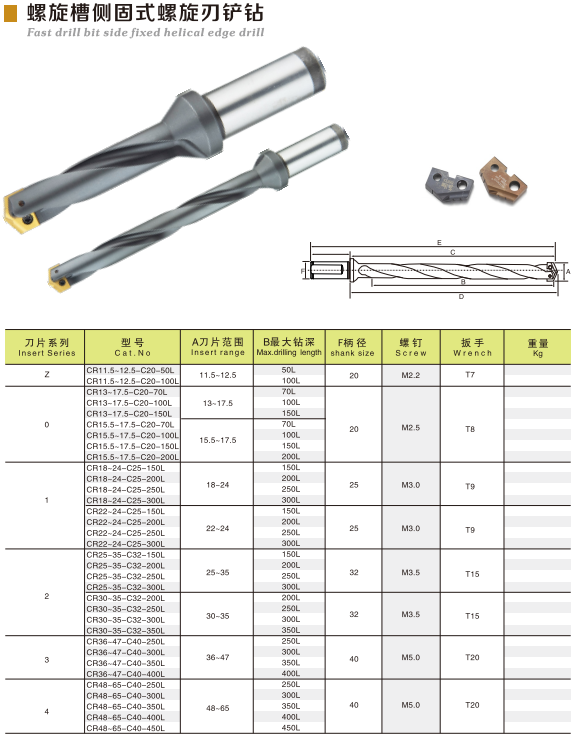
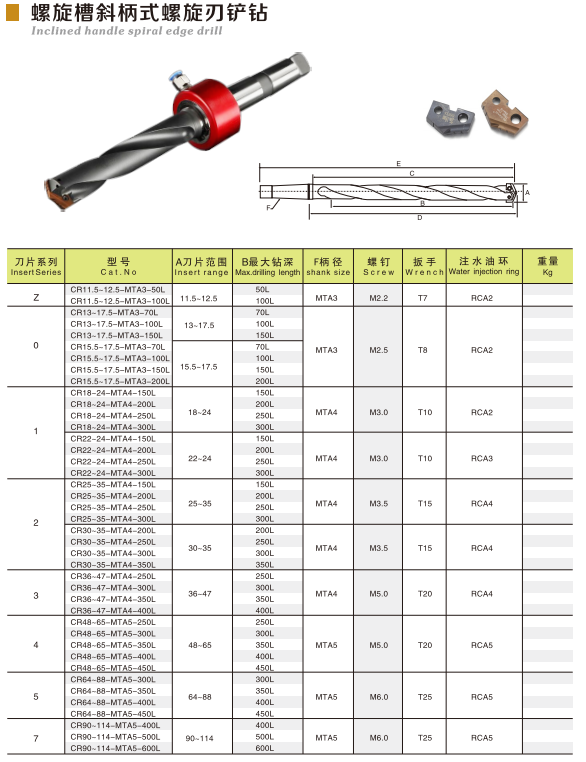
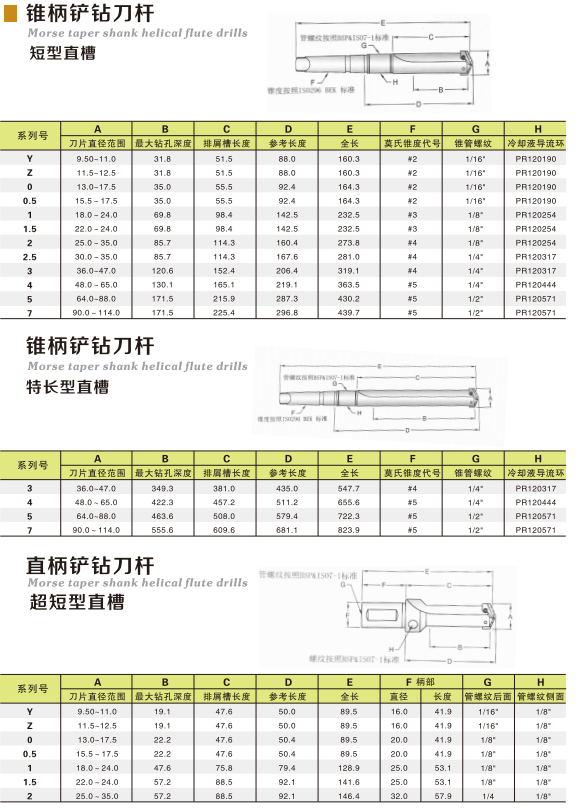
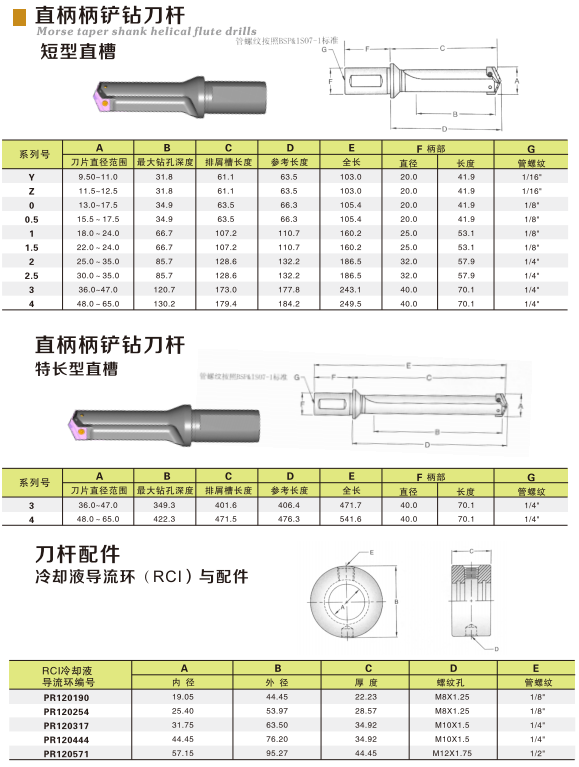
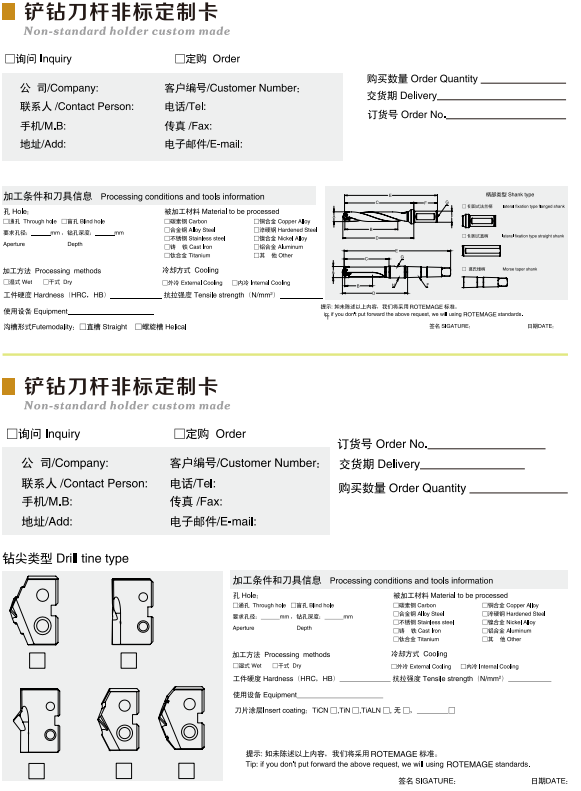