제품 소개
스페이드 드릴 인서트
다양한 재질의 작업물을 가공할 때는 가공에 맞는 다양한 재질의 스페이드 드릴 비트를 선택하세요.
스페이드 드릴 인서트 소재는 다음과 같이 구분됩니다.
1. 카바이드(Φ9.5mm~Φ47.5mm)는 발저스 코팅을 채택
2. 분말 고속도강 (Φ9.5mm~Φ114.0mm)
3. 코발트함유 고속도강(Φ9.5mm~Φ114.0mm)
다양한 재질의 작업물을 가공할 때는 가공에 맞는 다양한 재질의 스페이드 드릴 비트를 선택하세요.
스페이드 드릴 인서트 소재는 다음과 같이 구분됩니다.
1. 카바이드(Φ9.5mm~Φ47.5mm)는 발저스 코팅을 채택
2. 분말 고속도강 (Φ9.5mm~Φ114.0mm)
3. 코발트함유 고속도강(Φ9.5mm~Φ114.0mm)
동일한 직경을 가진 세 가지 재료의 인서트를 동일한 스페이드 드릴 아버에 설치할 수 있습니다.
이를 통해 고객의 공구 홀더 구매 비용을 대폭 줄일 수 있습니다.
이를 통해 고객의 공구 홀더 구매 비용을 대폭 줄일 수 있습니다.
1. 수직 드릴 및 방사형 드릴에는 고속강 및 분말 고속강 인서트를 사용하는 것이 좋습니다.
카바이드 인서트를 사용하는 것은 권장되지 않습니다. 공작 기계 속도가 낮고 강성이 좋지 않으며 틈새가 커서 카바이드 인서트가 쉽게 점프할 수 있습니다.
2. 모든 스페이드 드릴 툴 홀더에는 중앙 물 배출구가 있습니다. 가능한 한 고압 내부 냉각수를 사용하는 것이 좋습니다. 이렇게 하면 인서트의 서비스 수명이 크게 연장되고 칩 제거에 더 도움이 됩니다.
3. 모든 스페이드 드릴 인서트는 칩 브레이커로 설계되었으며, 가공된 철 칩은 모두 작은 칩입니다. 전통적인 트위스트 드릴로 가공된 긴 칩과 비교할 때, 작은 칩은 칩을 깨기 위해 후퇴할 필요 없이 제거하기가 더 쉽습니다. , 바닥까지 치면 가공 시간을 단축하고 가공 효율을 향상시킬 수 있습니다.
4. 스페이드 드릴 인서트는 셀프 센터링 기능을 가지고 있으며, 양날 인서트는 대칭적이고 균일한 힘을 견디므로 깊은 구멍을 가공하는 데 적합합니다.
스페이드 드릴링 가공 매개변수 계산
드릴링 고속강 및 분말 고속강 인서트의 선형속도는 20~40m입니다.
카바이드 인서트의 선형 속도는 50~60m이고, 스페이드 드릴 인서트의 회전당 이송은 회전당 0.1~0.6mm에 도달할 수 있습니다.
드릴링 고속강 및 분말 고속강 인서트의 선형속도는 20~40m입니다.
카바이드 인서트의 선형 속도는 50~60m이고, 스페이드 드릴 인서트의 회전당 이송은 회전당 0.1~0.6mm에 도달할 수 있습니다.
A. 드릴링 속도 계산 공식은 다음과 같습니다: S=VC*1000/3.14/Dc
(S는 회전속도, Vc는 선형속도, Dc는 인서트 직경)
B. 사료 계산 공식은 다음과 같습니다: Vf=Fr*S
(Vf는 이송, Fr은 드릴당 이송, S는 회전 속도)
C 처리 시간 공식은 다음과 같습니다: Tc=H/Vf*60
(Tc는 처리시간, H는 구멍깊이, Vf는 이송량)
(S는 회전속도, Vc는 선형속도, Dc는 인서트 직경)
B. 사료 계산 공식은 다음과 같습니다: Vf=Fr*S
(Vf는 이송, Fr은 드릴당 이송, S는 회전 속도)
C 처리 시간 공식은 다음과 같습니다: Tc=H/Vf*60
(Tc는 처리시간, H는 구멍깊이, Vf는 이송량)
속도 및 이송 계산 예
가공직경 20mm, 깊이 100mm,
분말 고속강 인서트를 선택하면 선형속도는 40m로 계산됩니다.
S=40*1000/3.14/20=636(분당 권장 드릴링 속도는
F600~650 정도)
Vf=0.2*636=127 (분당 권장사료량은 S110~130)
에 대한)
Tc=100/127*60=47 (처리시간은 약 50초)
가공직경 20mm, 깊이 100mm,
분말 고속강 인서트를 선택하면 선형속도는 40m로 계산됩니다.
S=40*1000/3.14/20=636(분당 권장 드릴링 속도는
F600~650 정도)
Vf=0.2*636=127 (분당 권장사료량은 S110~130)
에 대한)
Tc=100/127*60=47 (처리시간은 약 50초)
사용상의 주의사항
1. 스페이드 드릴을 사용할 때는 중앙에 물 배출구가 있어야 하며, 이는 공구 수명을 연장하고 더 나은 칩 제거 효과를 제공하는 데 도움이 됩니다.
2. 처음으로 도구를 사용할 때 도구를 입력하고 드릴링을 준비할 때 매개 변수를 10-15% 낮추는 것이 좋습니다.
3. 길이가 8D를 초과하는 경우, 사용하기 전에 동일한 직경의 파일럿 홀을 미리 드릴링해야 합니다. 파일럿 홀의 깊이는 홀 직경의 1-2배로 드릴 비트 편차 문제를 크게 줄일 수 있습니다.
4. 굴착된 철슬래그는 일반적으로 파편 모양입니다. 가공 중 철슬래그의 소리와 모양에 주의하십시오. 철슬래그의 띠가 나타나면 사용 매개변수를 제때 조정해야 합니다.
5. 관통 구멍을 가공할 때는 구멍이 뚫릴 때 공구를 수축합니다. 수축할 때 인서트가 작업물에 부딪혀 손상이 발생하는 것을 방지하기 위해 인서트를 구멍 밖으로 완전히 확장하지 않도록 주의하세요.
1. 스페이드 드릴을 사용할 때는 중앙에 물 배출구가 있어야 하며, 이는 공구 수명을 연장하고 더 나은 칩 제거 효과를 제공하는 데 도움이 됩니다.
2. 처음으로 도구를 사용할 때 도구를 입력하고 드릴링을 준비할 때 매개 변수를 10-15% 낮추는 것이 좋습니다.
3. 길이가 8D를 초과하는 경우, 사용하기 전에 동일한 직경의 파일럿 홀을 미리 드릴링해야 합니다. 파일럿 홀의 깊이는 홀 직경의 1-2배로 드릴 비트 편차 문제를 크게 줄일 수 있습니다.
4. 굴착된 철슬래그는 일반적으로 파편 모양입니다. 가공 중 철슬래그의 소리와 모양에 주의하십시오. 철슬래그의 띠가 나타나면 사용 매개변수를 제때 조정해야 합니다.
5. 관통 구멍을 가공할 때는 구멍이 뚫릴 때 공구를 수축합니다. 수축할 때 인서트가 작업물에 부딪혀 손상이 발생하는 것을 방지하기 위해 인서트를 구멍 밖으로 완전히 확장하지 않도록 주의하세요.
제품 세부정보
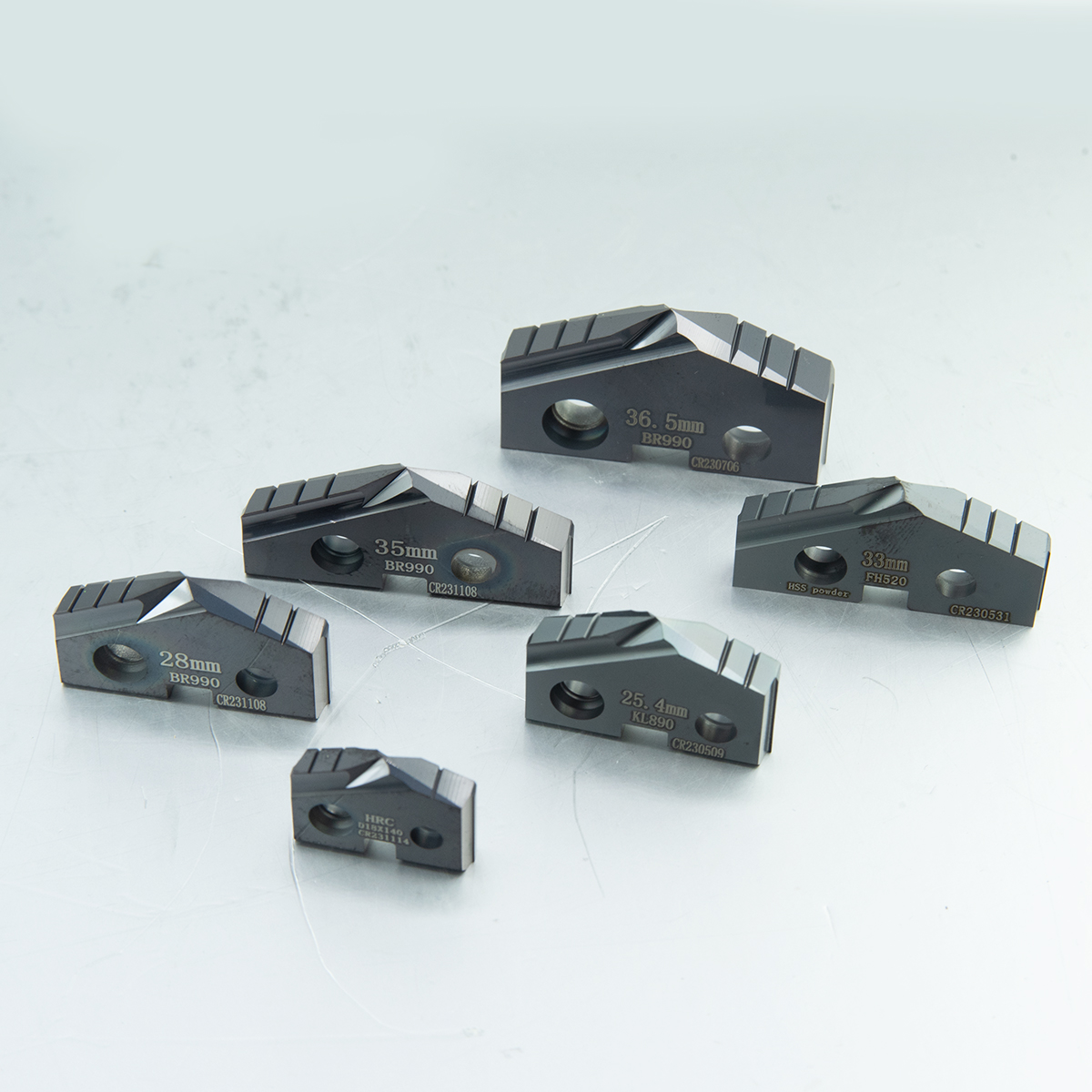
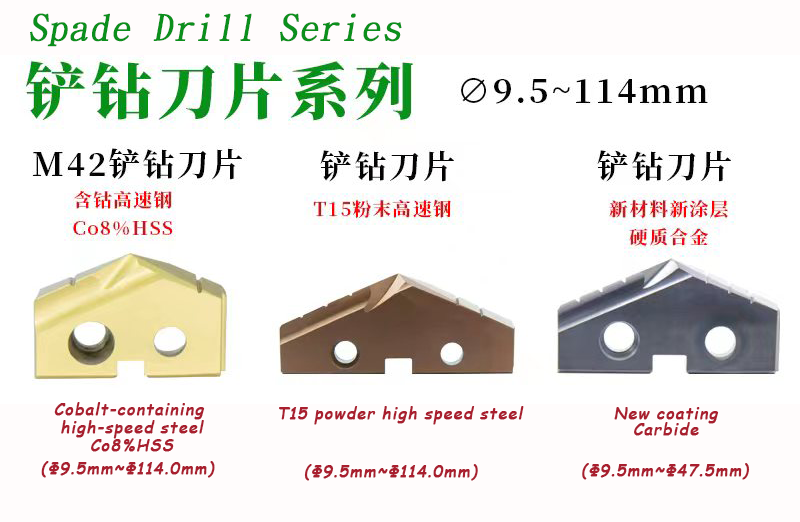
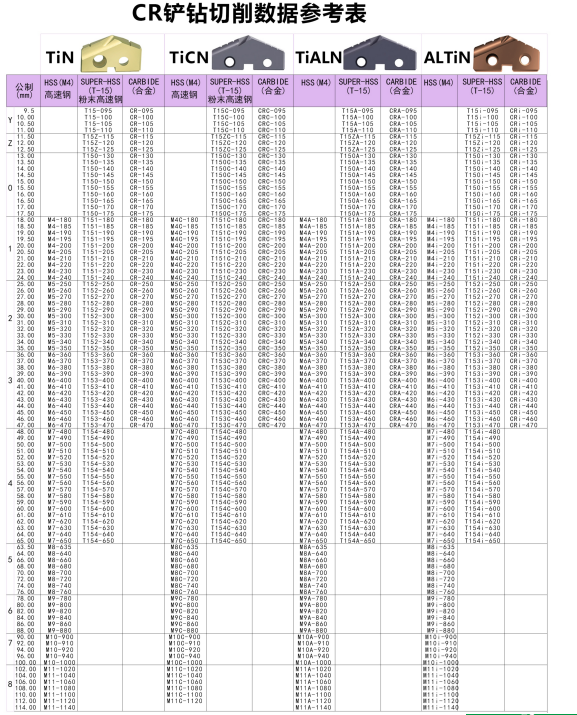
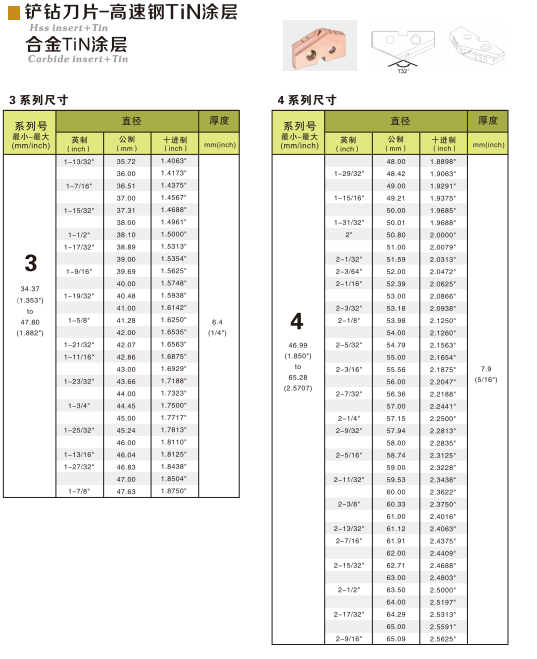
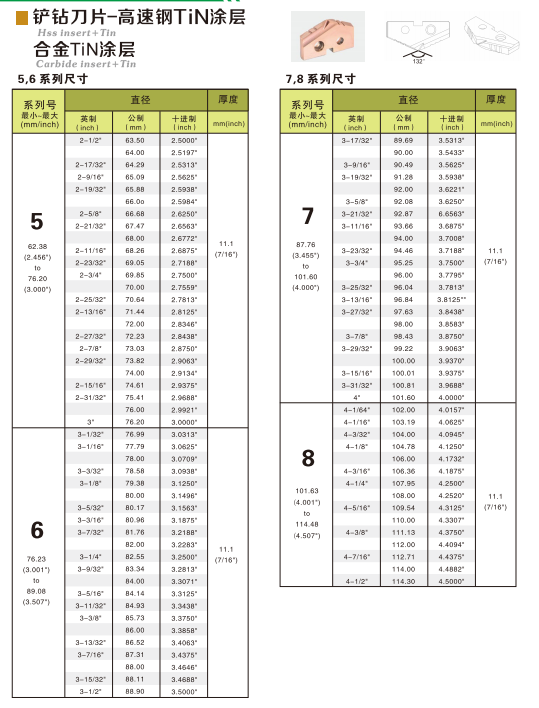
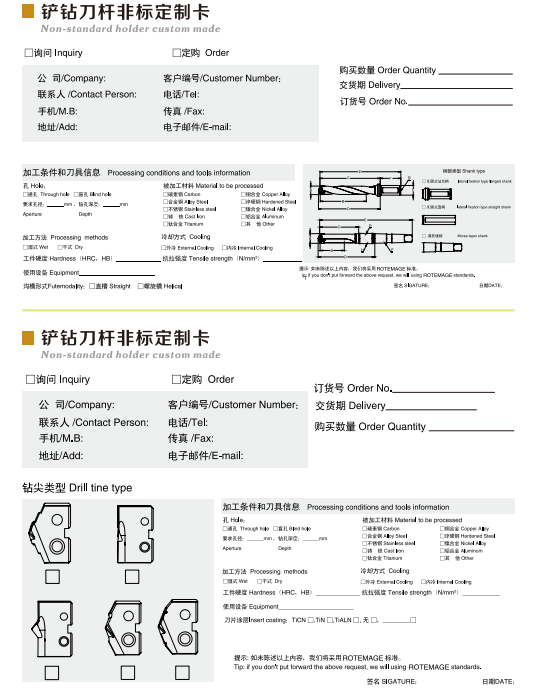